CHALLENGES
Funded Projects, Call 7

Elastomeric fibers based on novel biopolymers
The project focuses on developing novel elastomeric fibers from biopolymers as a sustainable alternative to synthetic fibers in textiles. Addressing the challenge of textile waste, the goal is to create recyclable, compostable, and cost-effective fibers, particularly for elastic cover yarns. Sulzer leads biopolymer development, while FHNW specializes in fiber spinning and characterization. The project exploring circular approaches for textile applications.
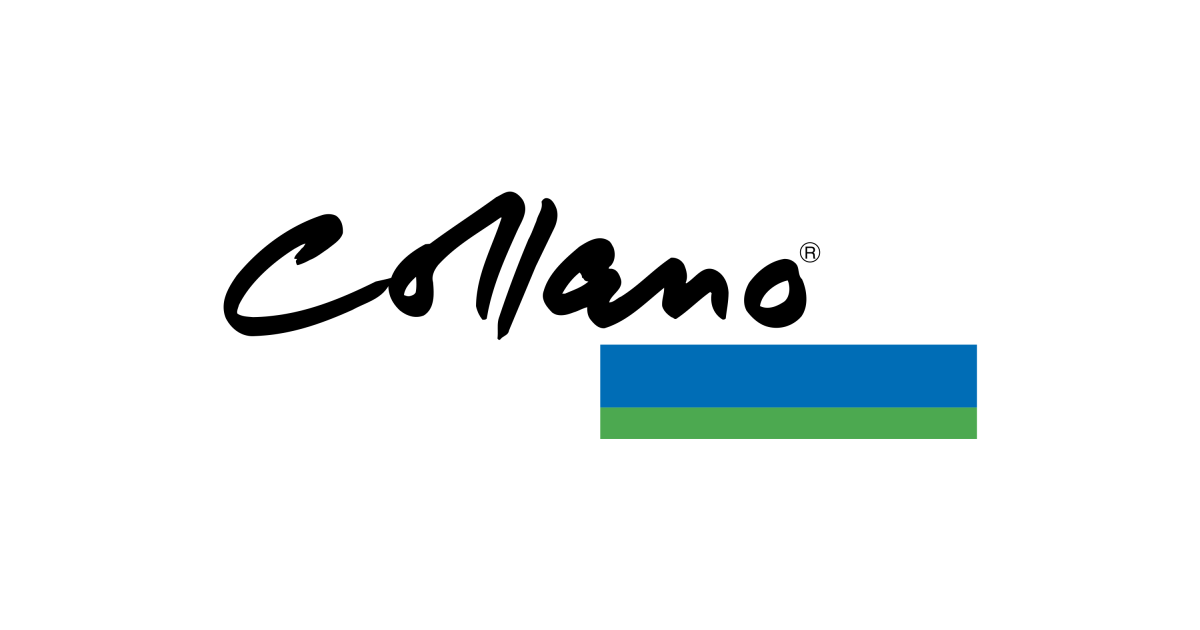
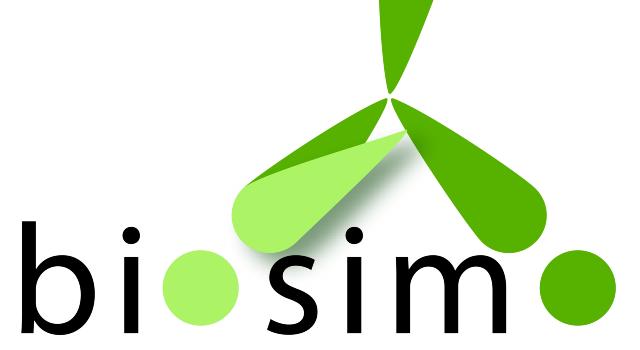
More Sustainable Production of New Green Monomers
Building on our 80-year legacy of innovation in sustainable adhesives, Collano proposes, together with Biosimo, a groundbreaking project to develop bio-derived monomers as replacements for petrochemical-based monomers. While bio-sourced monomers that contribute to stiffness are more readily available, e.g., isobornyl methacrylate from pine resin, “softer” monomers come from palm oil sources that could interfere with the food chain. Our ambitious goal is to create new bio-sourced monomers, which would be a remarkable achievement in the industry. Recently, Collano launched a pressure-sensitive adhesive for brand protection labels, based on renewable monomers. Due to the structure of the new monomer, this bio-adhesive outperformed petrochemical counterparts, offering a more secure product against counterfeiting. Unfortunately, these monomers are based on cocoa bean or palm oil kernel, competing with food and potentially with the new EU deforestation regulation. Other more exotic monomers are no longer available. E.g., itaconic acid and di-butyl itaconate, won by the fermentation of sugar with fungi. Unfortunately, the supply to Europe is very difficult, hindering new truly sustainable adhesive products. We want a green revolution in Switzerland, pulling raw materials manufacturing back to Switzerland.
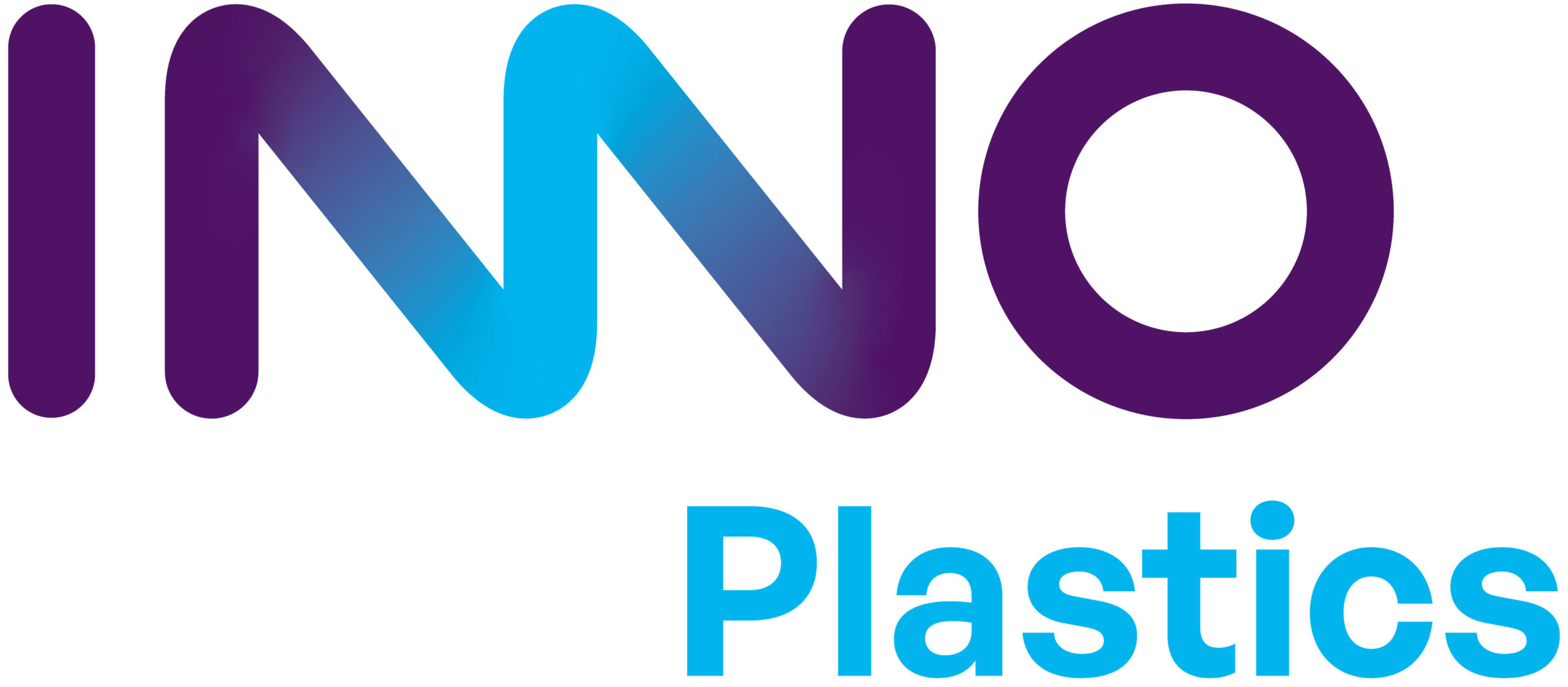
All in One Solution: Revolutionizing Plastic Recycling
Modern life would be unthinkable without plastic, yet plastic waste’s environmental impact must be drastically reduced Increased mechanical recycling is key to conserving resources, reducing CO2 emissions, and strengthening Switzerland’s supply security for polymer materials.
To boost recycling rates and the use of recycled materials, innovative recycling technologies are needed. Particularly high-quality, closed-loop applications call for state-of-the-art installations and new technological equipment. However, Switzerland faces challenges due to the wide variety of polymers used and the relatively small quantities collected, making large-scale recycling plants difficult to implement.
The key challenge is achieving local plastic loops for diverse polymers without substantial investment in new facilities that struggle with low input volumes. This project aims to pave the way for an ‘all-in-one’ recycling solution that integrates multiple polymers within a single installation. By developing a multi-polymer recycling system, InnoPlastics AG aspires to set a new benchmark for circularity in plastics, fostering innovation and driving sustainability across the industry.
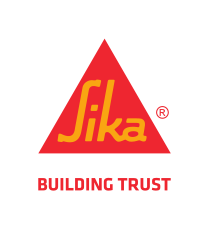
Membrane for thermal energy storage
Thermal energy storages are one of the key technologies to solve the energy crisis, particularly the winter gap. One of the most popular solutions is the so-called pit-storage, a large man-made hole in the ground which is sealed off from the earth by a polymer liner. This liner should prevent the water from leaking into the environment. But state of the art liners exhibit high water vapor diffusion rates and therefore leak warm water into nature. To change this, we need new technologies for these liners, but there is no test standard in place to test water vapor diffusion rates at higher temperature. In this project we will develop such a test method and enable innovative new solution for liners for thermal energy storages.v
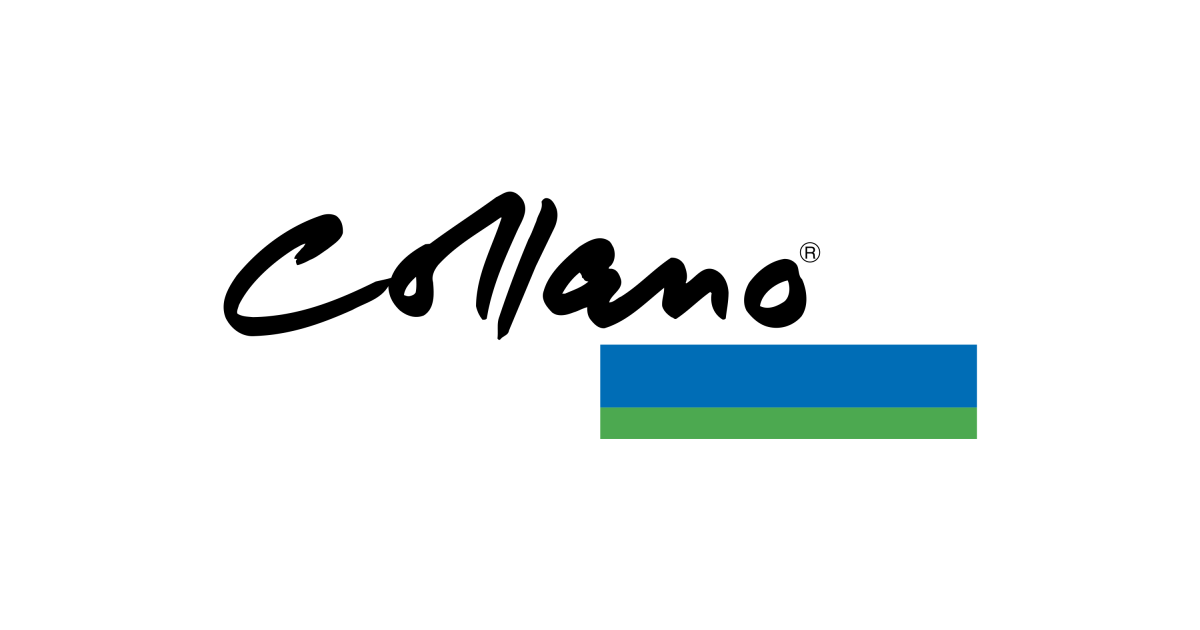
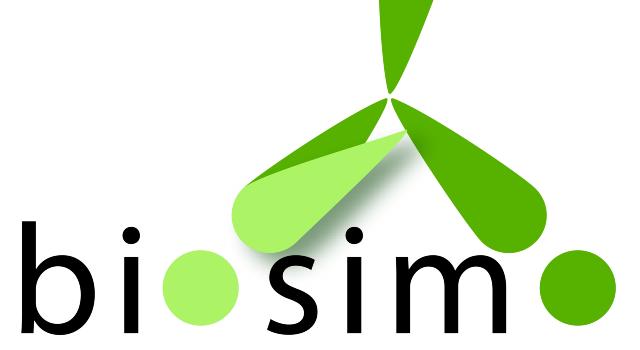
More Sustainable Production of 2-Ethylhexanol
Building on our 80-year legacy of innovation in sustainable adhesives, Collano proposes, together with Biosimo, a groundbreaking project to develop bio-derived monomers as replacements for petrochemical-based materials, specifically 2-ethylhexyl acrylate (2-EHA), for emulsion polymerization. While bio-sourced monomers that contribute to stiffness are more readily available, our ambitious goal is to create a bio-sourced 2-EHA equivalent, which would be a remarkable achievement in the industry. This initiative aligns with our commitment to environmental stewardship and positions Collano at the forefront of the green chemistry revolution in Switzerland. As a small, agile player in the adhesive world, our strength lies in our ability to target niche, high-performance markets with bold, innovative approaches. E.g., the global wood adhesives market, valued at $4.76 billion in 2020 and projected to reach $6.55 billion by 2027, is driven by increasing demand for eco-friendly products. Our project capitalizes on this trend, offering significant market potential and a distinctive competitive advantage.
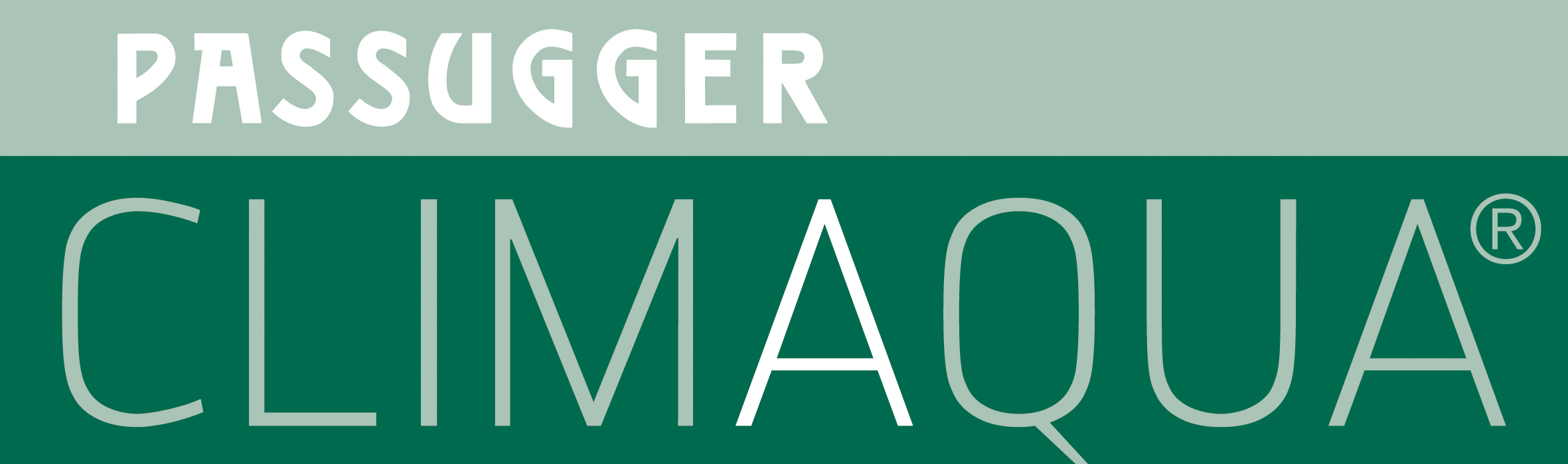
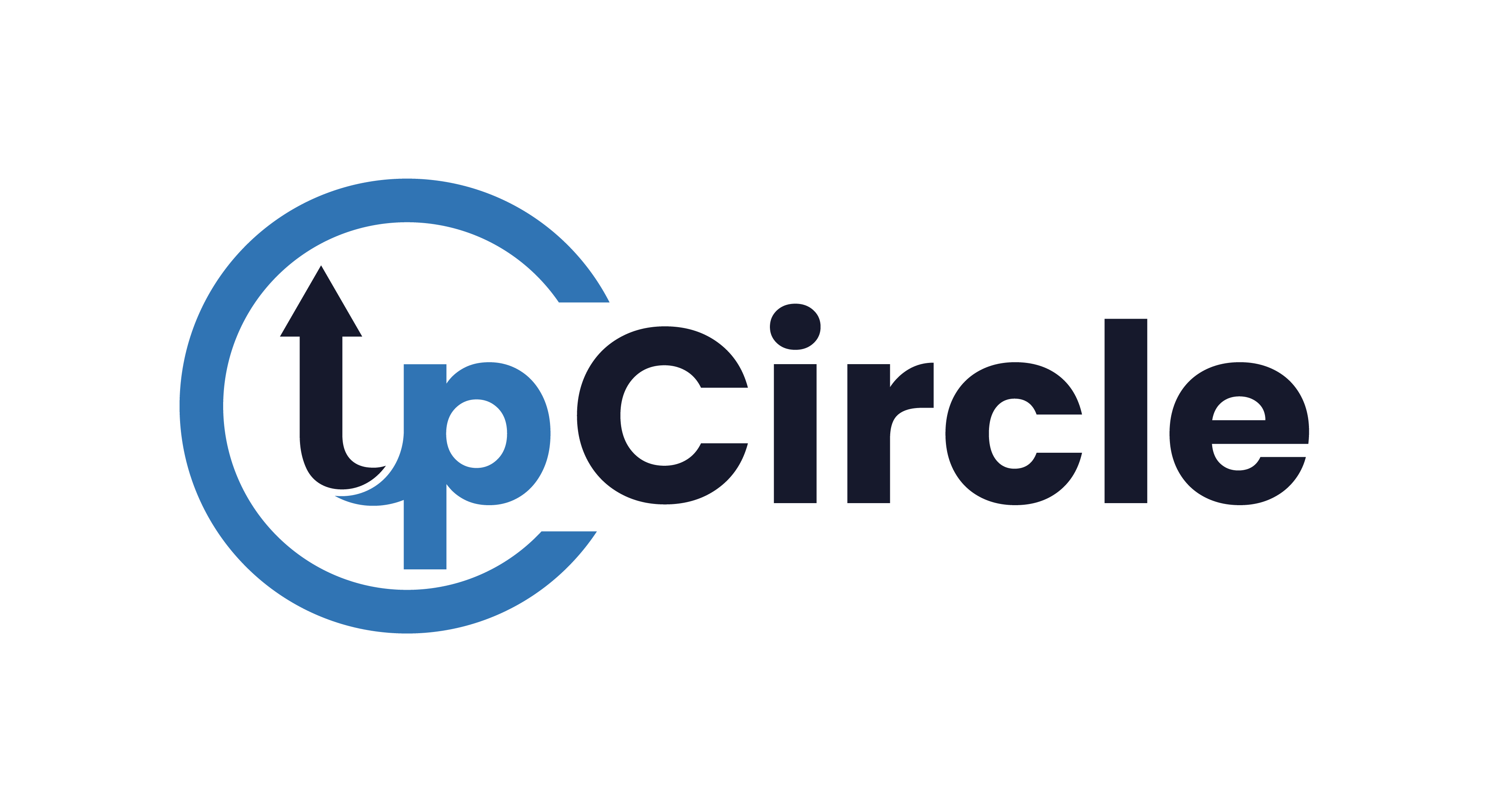
SmartBaler: Enhancing Recycling Efficiency and Reducing Carbon Emissions in Supermarket Logistics
The SmartBaler project aims to optimize waste management and reduce carbon emissions at return logistics center of large retailers by integrating ETH Zurich’s AI-driven Bale Monitoring System. This innovative solution analyzes waste bale composition in real-time, enabling improved routing, contamination detection, and recycling efficiency. By making data-driven decisions at the source, the project minimizes unnecessary transport emissions and enhances recycling outcomes. Partnering with Allegra Passugger, this initiative showcases a scalable approach to smarter resource recovery, with the potential to revolutionize waste management in logistics centers worldwide.
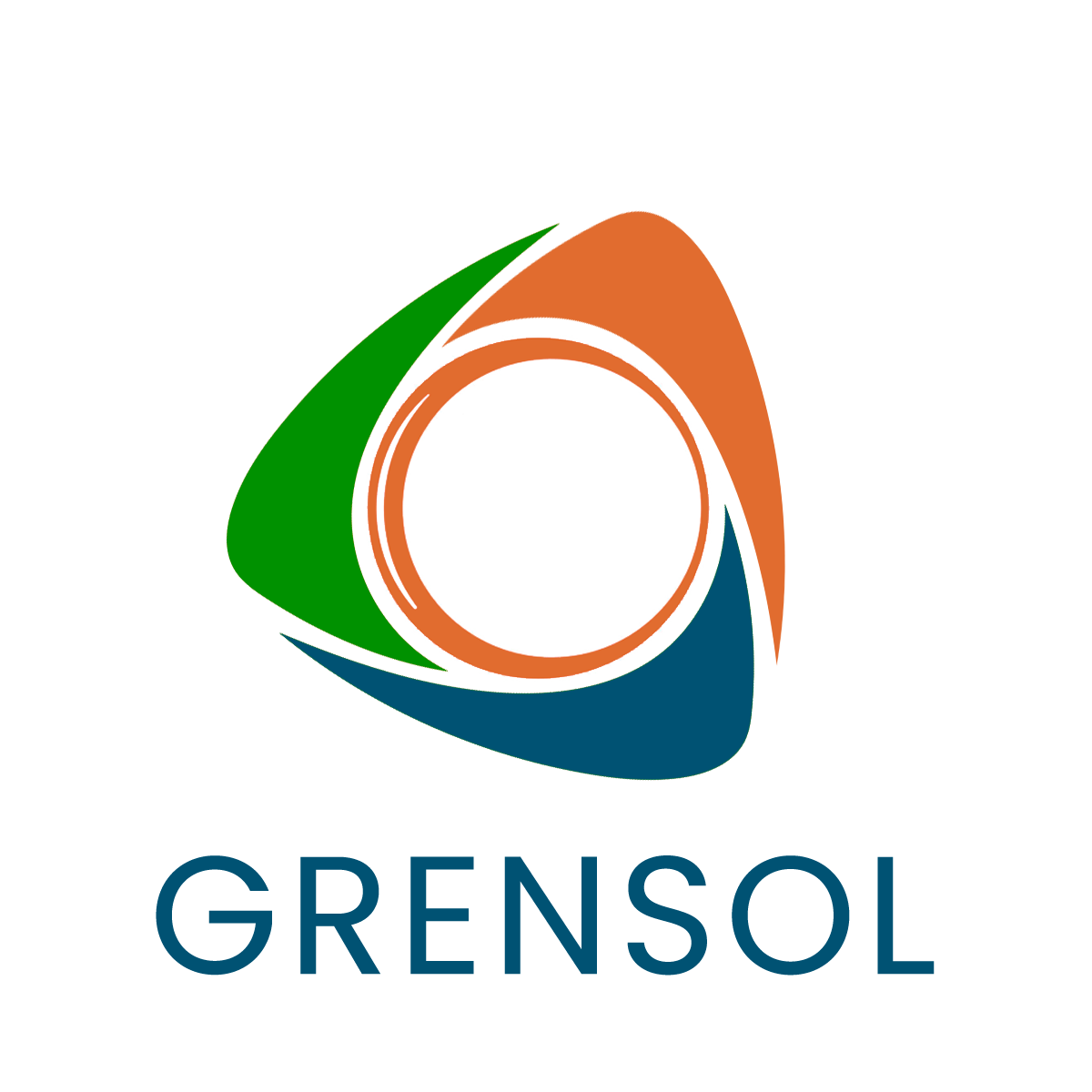
Generating Applications for Grensols Recycled Carbon
Grensol is revolutionizing waste management by repurposing residues from used car recycling, which traditionally end up in landfills or incinerators, leading to pollution and resource wastage. Through an innovative two-step process, Grensol first separates valuable metals and minerals for reuse, and then applies its proprietary Photolysis technology to convert remaining hydrocarbons into syngas and carbon black. This sustainable approach not only recovers high-value raw materials but also aligns with circular economy principles, reducing environmental impact while unlocking economic potential. We are also exploring ways to extend this technology to process electronic scrap and demolition waste plastics.
A key challenge for Grensol lies in finding commercial applications for the carbon black recovered from the Photolysis process, as the market imposes strict quality standards. To address this, we are testing carbon black as an additive in 3D printing polymers, allowing for direct feedback on product specifications and enabling refinement to meet industry requirements. This serves as an entry point for the material’s commercialization in small-scale applications, with the potential to scale up for broader use in injection molding and other high-volume manufacturing processes.
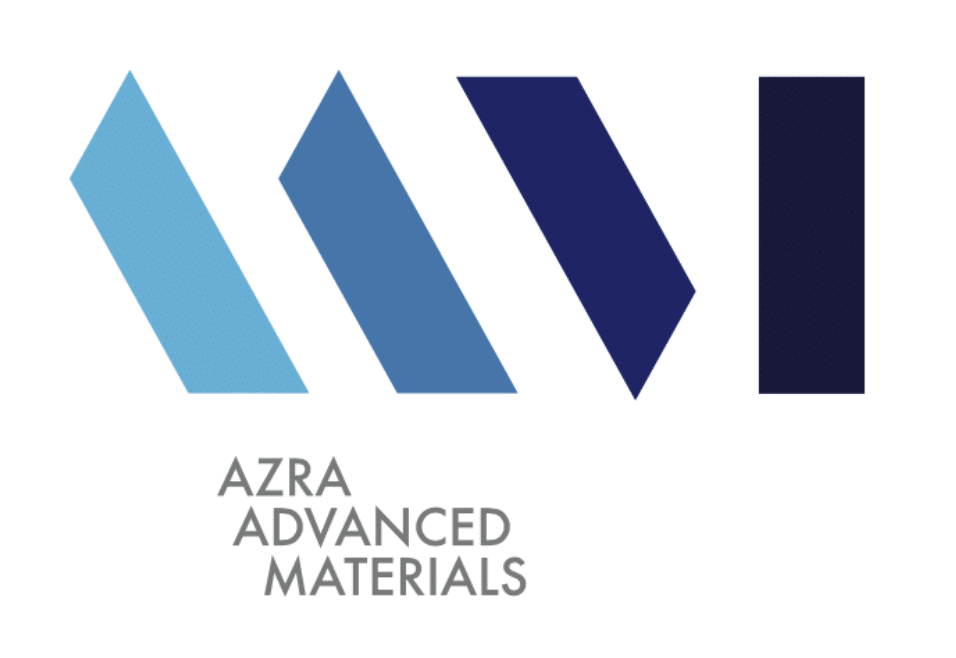
New class of polymeric coating solutions for CO₂ capture, transportation and storage
Carbon capture, utilization, and storage (CCUS) is expanding due to climate goals and investment opportunities. Supercritical CO₂ (s-CO₂) transportation via pipelines or vessels are the most efficient methods, but corrosion of carbon steel caused by contaminants (SOx, NOx, H2S, O2) poses a major challenge. Existing polymeric coatings are not resistant to direct contact with s-CO₂, which compromises their integrity. Azra Advanced Materials aims to develop a new class of coatings capable of withstanding long-term exposure to s-CO₂, enabling the safe and scalable deployment of CCUS solutions while supporting carbon credit certification.
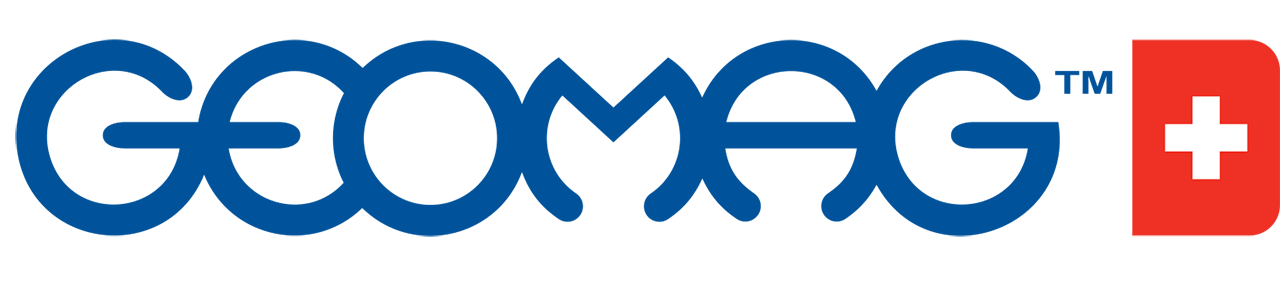
Development of a synthesis process towards polyesters
Geomag and Federlegno see a unique opportunity in developing a business based on tannins in Switzerland. Tannins, a class of polyphenolic compounds found in various plants, are already used in the production of wood adhesives, offering a natural and sustainable alternative to synthetic adhesives. However, beyond these specific applications, tannins show significant potential as monomers and copolymers for biobased polymers.
Geomag is particularly interested in tannin-based polymers for their potential to create sustainable plastic toys, enhancing the educational value of our products. The Innobooster project represents a starting point for the next generation of Geomag World magnetic toys.
Federlegno Ticino supports this challenge with the aim of encouraging new circular businesses, leveraging a Swiss value chain.
The challenge we address is the development of a synthesis process towards polyesters, overcoming uncertainties related to the polymerization costs of tannins and ensuring good mechanical properties and processability. Specific research is needed to identify the chemical route to obtain tannin-polymers at reasonable costs while maintaining high mechanical performance and workability.
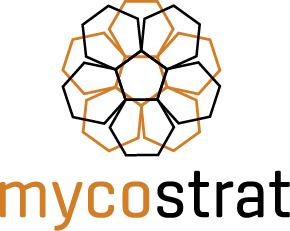
Replacement of polystyrene insulation boards with pollutant-free and recyclable composites
Polystyrene insulation has long been favored for its affordability and insulating properties, but its environmental and health drawbacks are undeniable. Made from petrochemicals, its production generates high CO₂ emissions, and once used, it lingers in landfills for centuries, with recycling rarely being a viable option. Worse, large amounts of polystyrene waste end up in oceans, breaking down into harmful microplastics that threaten ecosystems and enter our food chain. Additionally, toxic flame retardants and hazardous fumes released during burning pose serious health risks. With increasing regulations and rising disposal costs, the construction industry urgently needs a sustainable alternative.
Enter mycelium-based insulation—a game-changer in green building materials. Mycelium naturally binds lignocellulose fibers from agricultural and forestry waste, creating a fully biodegradable, high-performance alternative to polystyrene. It offers excellent insulation, regulates moisture, and is inherently fire-resistant—without the need for toxic additives. Even better, it can be composted or regrown at the end of its life, aligning perfectly with circular economy principles.
The challenge now is scaling up. To compete with traditional materials, production processes must become more efficient and cost-effective while ensuring consistency at an industrial level. By overcoming these hurdles, mycelium-based insulation can revolutionize sustainable construction—offering a future where insulation is not only high-performing but also truly regenerative.
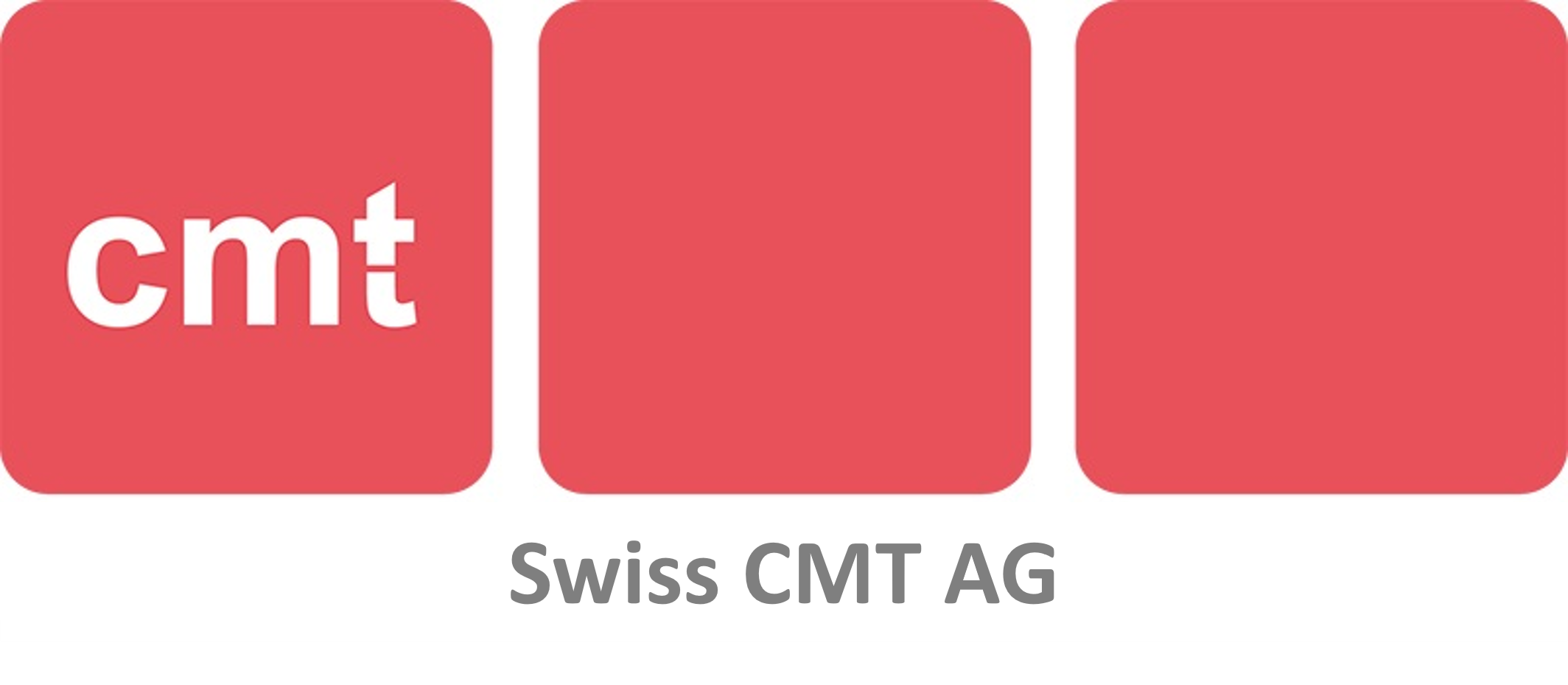
Natural flame-retardant additives for composites
Swiss CMT AG is a well-known developer of sustainable lightweight (composites) materials and processes.
In this project we are focusing on developing natural-based flame-retardant additives for our sandwich panel and part manufacturing customers. Our product idea is based on residuals from the European rice and wood industry, in which we convert Rice-Husk and Tannin-Extracts into a suitable additive that will be compounded with modern resin systems.
First independent, non-scientific laboratory trials showed some promising behaving, especially in the combination with our bio-based SolidResin system.
In the need of a large bandwidth of competences from compounding and composites characterization to fire-testing, we are confident to tackle this challenge together with specialists.
Projects, Call 6
100% bio-based and biodegradable lightweight sandwich structures
Sandwich structures achieve very good mechanical properties with a comparatively low weight. This benefits the life cycle assessment of the component during the utilisation phase. If bio-based materials are used, this also has a positive effect on the CO2 balance of the component during production. However, sandwich components are a challenge for the recycling process, as the mechanical properties are achieved by permanently bonding materials with different properties together. The aim is therefore to investigate promising material combinations and, where necessary, to further develop existing materials so that simple material recycling as well as thermal recycling and biodegradability are possible in sandwich construction. Promising applications are also to be identified on the basis of a characterisation of such components.
Extraction and utilization of biopolymers from macroalgae
Open Climate Solutions wants to encourage the use of biopolymers derived from certain macroalgae in a variety of plastics applications. Macroalgae from both marine and freshwater ecosystems, such as seaweed and stonewort (respectively), can be a sustainable resource if obtained from eco-conscious operations. In addition to improving water quality and supporting biodiversity, these sources of biomass close nutrient loops and thus contribute to a circular economy, effectively turning waste into valuable goods.
Furthermore, the possibility of producing a variety of co-products from the same kilogram of biomass by splitting and cascading the input into multiple streams presents a significant opportunity for highly efficient resource utilization. Given macroalgae are already used in a variety of applications including food, nutraceuticals, pharmaceuticals and agriculture, with new uses emerging regularly, it follows that a targeted effort to process certain macroalgae obtained from sustainable sources will undoubtedly yield clever, environmentally friendly uses.
The challenge aims to explore bioprocessing methods to derive high-value biopolymers from this microalgal biomass for sustainable bioplastic production while ensuring compatibility with co-production. This holds great potential for various applications. Additionally, the challenge will identify and preliminarily test downstream processes that can utilize these components effectively.
Open Climate Solutions can provide various sustainably sourced macroalgae and would welcome the opportunity to collaborate with research partners with expertise in various processing methods to work towards solving these challenges.
Re-mediation: Recycling materials from landfill plastics
Initial situation: By 2050, the mass of plastic materials in landfills and in nature is estimated to reach 12,000 tonnes worldwide. These plastics will be removed from the material cycle and will lose value and quality if landfilled for a longer period of time. In order to make landfill remediation more economically viable, a new area of application is needed for contaminated materials as an alternative to incineration. The Tännlimoos landfill site is operated by JURA and contaminated fractions are currently being remediated. During the remediation of the landfill site, 7000 tonnes of combustible material are sorted out each year and then incinerated in a waste incineration plant. A proportion of this combustible material consists of plastics, mainly from the construction industry. These plastics cause high costs for JURA, as the calorific value of the fraction is not ideal. This is partly due to mineral contamination, but also to the high proportion of flame retardants. In this project, JURA wants to find out whether these plastic materials could be recycled.
Project content: The aim of this feasibility study is to investigate whether the production of high-quality recycled materials from landfill plastics is feasible and viable. In this project, plastic materials from the contaminated sites of the Tännlimoos landfill are to be processed in such a way that they can be reused technologically.
PHAs in Action: Putting Polyhydroxyalkanoates Under Scrutiny
Ems-Chemie is looking to expand its green portfolio. While the EMS production site is CO2 neutral, the majority of its polymers originate from oil-based, non-renewable sources. EMS seek to rectify this across multiple different product segments:
- Replacing current oil-based co-polyesters with CO2neutral alternatives (target segments: powders, injection moulding and films and webs)
- Compounding standard products with a degree of compatible bio-based/CO2neutral alternatives to decrease the overall CO2 footprint (segments: injection moulding, films and webs)
- Utilization of alternative bio-based or CO2derived monomers (e.g. bio-based polycaprolactam – target material segments: automotive, adhesives)
- Replacement of standard carbon fibres with recycled carbon fibres for metal replacing applications (e.g. Grivory HT materials 50% CF –> 50% r-CF)
EMS possesses the infrastructure needed to take this vital step, however implementation of such initiatives is problematic, especially regarding product quality consistency. EMS needs expert partners to develop solutions to these problems and evaluate their performance. With these partnerships, EMS can leverage its already established CO2 neutral/negative production processes with innovative CO2 negative/neutral feedstocks for a powerful environmentally conscious product range.
Development of water and grease resistand barrier coating from wood
Bloom Biorenewables has developed and scaled the aldehyde assisted fractionation (AAF) technology that allows to efficiently extract and isolate lignin from lignocellulosic biomass. The isolated lignin presents a near-native structure, meaning it is not condensed during the extraction process giving it similar properties to those lignin presents in nature. Inspired by these lignin characteristics we are developing a bio-based solution for the packaging industry inspired by nature’s natural protection mechanisms.
Projects, Call 5
Grensol Group – Recycling Automotive Plastics, Without Emissions
Grensol is developing a novel solution to recycle mixed plastic waste generated during the recycling of end-of-life cars and domestic appliances. Our patent-pending photonic process essentially ‘unmanufactures’ plastic waste, breaking it down into its fundamental building blocks: carbon and hydrogen. These can then be reused as feedstock for new plastic manufacturing. This method proves especially valuable when dealing with input plastic waste that consists of mixed polymer types or is contaminated with impurities. We are thereby facilitating a circular economy for tough-to-recycle plastics. We have demonstrated the success of this approach on a laboratory scale and are now looking to scale it up for industrial use.
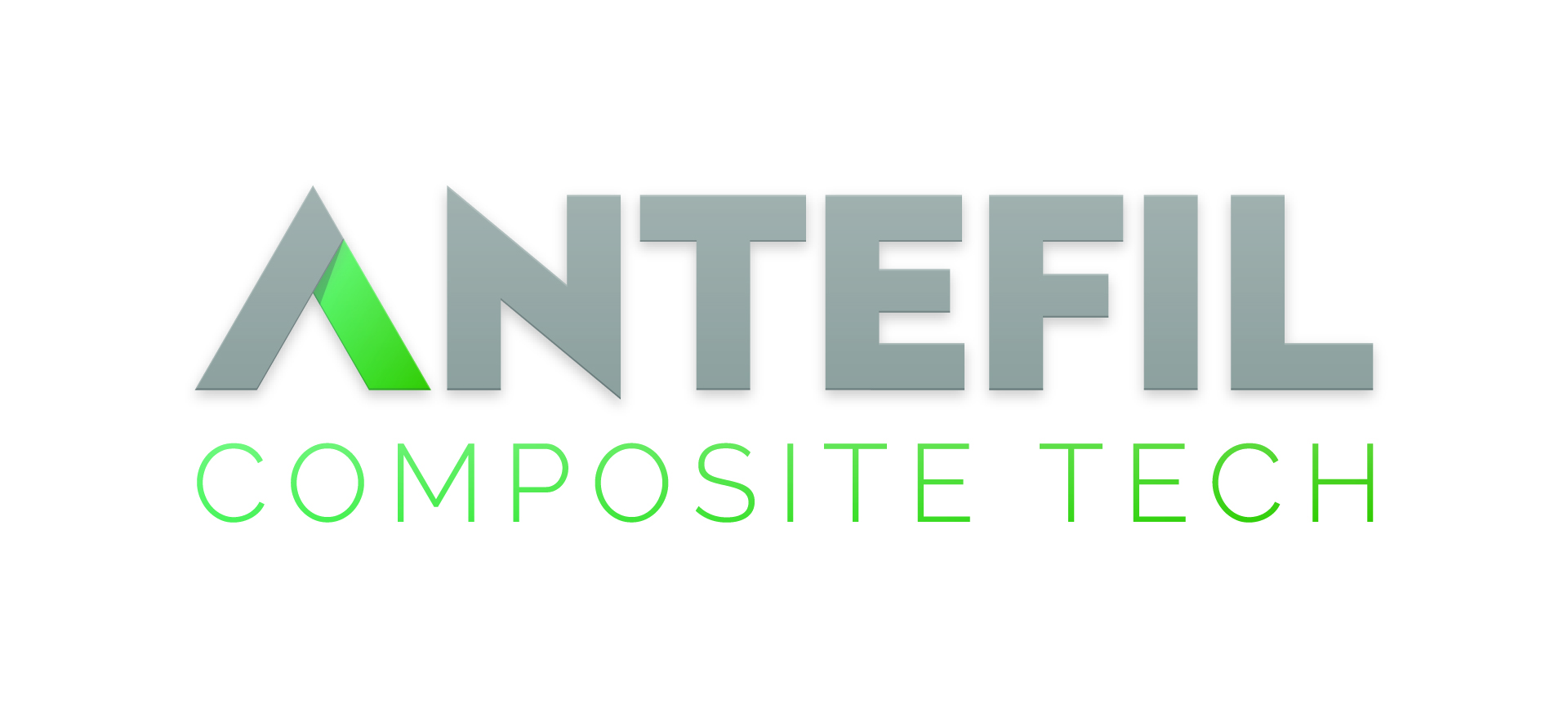
Antefil – Overmoulding of glass/semicrystalline hybrid fibre inserts
Antefil Composite Tech produces hybrid fibre rovings and yarns, consisting of glass filaments which are individually coated with a thermoplastic matrix material. This coating is applied in-line with the melt spinning of the glass fibre, which ensure a complete surface coverage and homogeneous distribution of the polymer on every fibre. Antefil intends to evaluate the use of such rovings as inserts for injection moulding. A previous study has yielded promising results for PMMA, even when inserting the fibres without pre-heating. A remaining challenge is to achieve a high surface quality. The proposed challenge focuses on applying this method to semicrystalline polymers and to yield high surface quality in a fast and energy-efficient process.
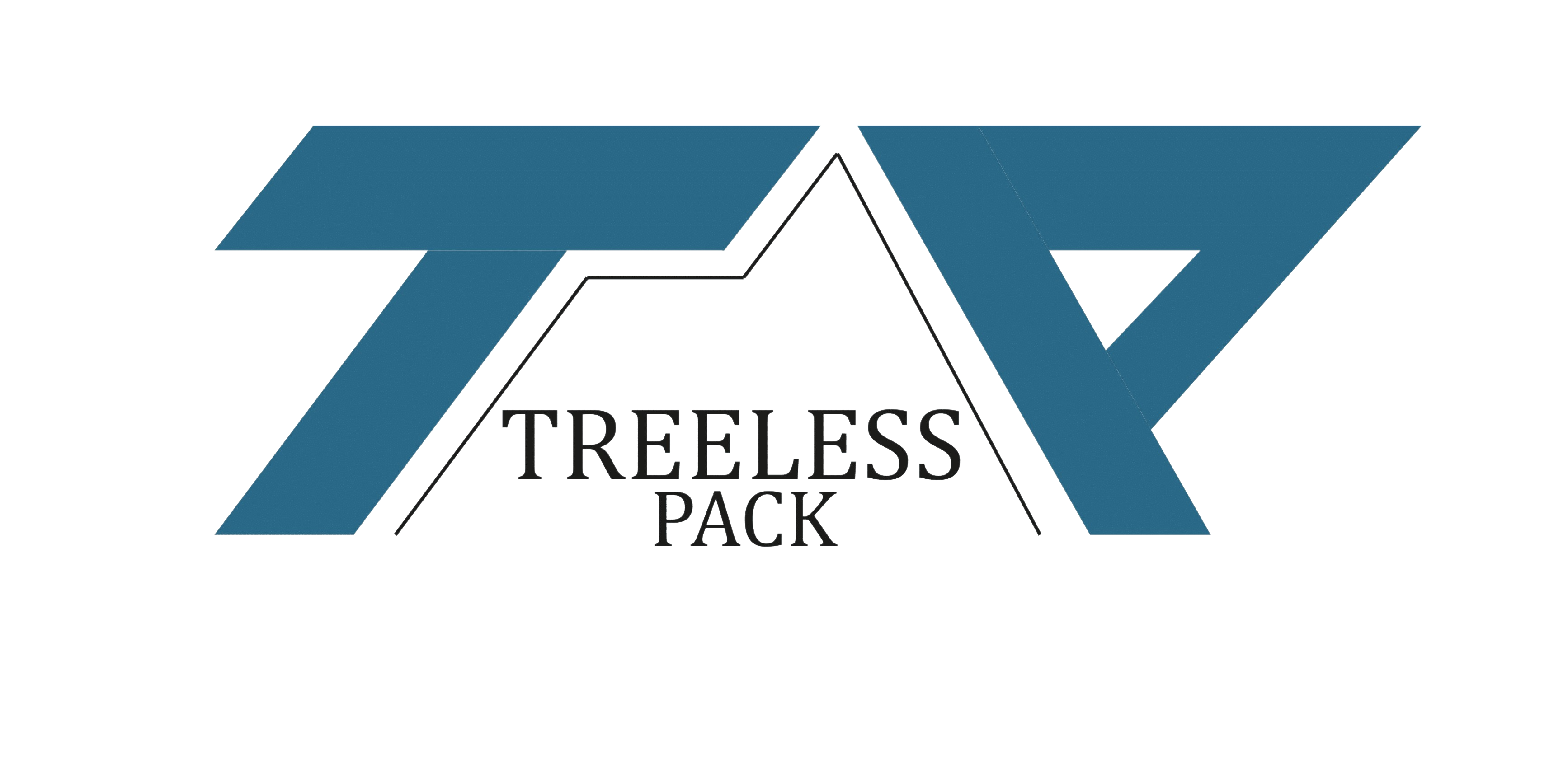
Treeless Pack with 2 individual challenges
Treeless Pack is on a mission to redefine sustainability in material production, focusing on microorganism-based nanocellulose as a green alternative to fossil-based products. By leveraging automated technology, organic waste and microorganisms, we reduce costs and environmental impact, avoiding traditional, emission-heavy methods of nanocellulose production. Treeless Pack aims to reveal the potential of nanocellulose and is constantly looking for innovative applications of its circular material.
Challenge – „Sealant“
In this call we aim to develop a silicone sealant application where the biomaterial could be applied to replace traditional fossil-based fillers such as silica and additionally benefit the final composition with improved mechanical and processing advantages. In collaboration with an industry leader in sealant development for the building materials, we seek for research partners specialized in adhesives and polymer modification and characterization.
Challenge – „Coating“
In preliminary studies we have shown our nanocellulose can be used to form a dense layer of tiny fibers which can act as a coating. Here, we look for a research partner, who would like to develop a method to deposit a coating layer on a substrate and evaluate its functionality. Furthermore, we search for industrial partners, for which a bio-based nanocellulose coating would be desired in their application.
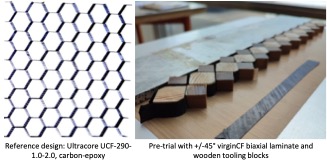
V Carbon/Connova – rCF Honeycomb
The idea of this project is to open a new market segment for recycled carbon fibre (rCF) in the space sector by making use of a unique property: The rCF material is believed to possess a uniform thermal expansion rate in x/y/z-direction, unlike virgin continuous UD-laminate. The material could be used in composite components where thermal expansion needs to be tightly controlled, such as in space applications, particularly in honeycomb sandwich panels for satellite solar arrays. Moreover, this would be the first approach of introducing recycled composite material into the space industry.
Projects, Call 4
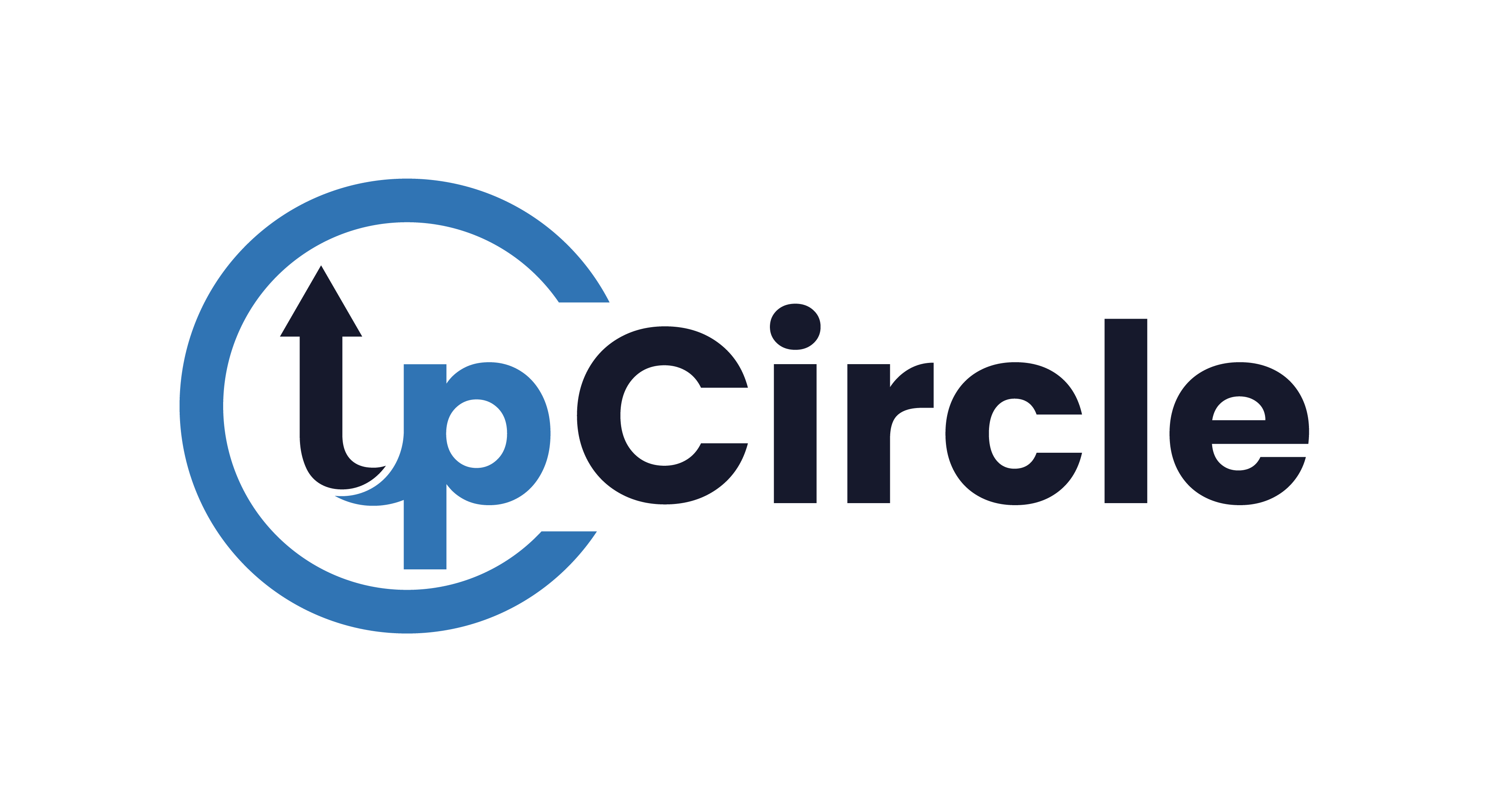
Quality Transparency in Baled Material: UpCircle’s Innovative Analytical Approach
The ETH-startup project UpCircle, in close collaboration with industry leaders such as InnoPlastics AG, addresses the challenges of the recycling industry with innovative solutions. They have observed that there are often misconceptions about the quality of recycled materials, which can lead to pricing debates and CO2-intensive processes. With already collected experience in the area of LDPE and HDPE, UpCircle aims to decipher the relationship between the external appearance and the content of bales using modern technologies. Their goal: A more sustainable and efficient recycling supply chain through improved quality analysis and increased process transparency. Want to be a part of this revolution?
Interested parties are warmly invited to get in touch with us!
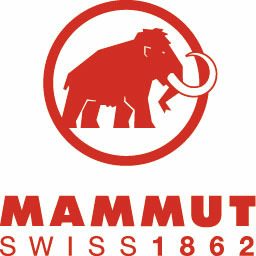
Natural, oil-based, coatings from resourcefully grown plants such as hemp, as replacement of chemical DWR (Durable Waterproof Repellent) finishes.
Traditional PFC-based Durable Water Repellents (DWRs) pose a threat to the environment due to their persistence and potential harm to ecosystems and human health. Although PFC-free DWRs were introduced as a solution, many still rely on synthetic chemicals and pose challenges in textile recycling processes, consequently contributing to plastic pollution. Growing consumer awareness and demand for eco-friendly products are driving the need and adoption of bio-based DWRs.
This challenge focuses on developing and adopting plant-based alternatives to PFC-free DWRs within the outdoor industry. The primary goal is to reduce plastic pollution associated with outdoor apparel production by addressing the recyclability of DWR treated outdoor garments through the use of bio based alternative water repellent finishes. The biodegradable nature of plant-based DWR solutions, may also ensure more readily breakdown in the environment, reducing the persistence of outdoor materials and mitigating plastic pollution.
Objectives of this challenge include identifying oil-based, sustainably and preferably locally grown plants for water repellent characteristics, developing DWR technologies based on identified plants, defining performance and consumer adoption requirements for bio-based DWR, performance testing, evaluating biodegradability, and promoting industry-wide adoption.
For this challenge, we would be looking to work together with experts in (bio-based) water-repellent coatings with facilities to develop new potential alternative solutions.
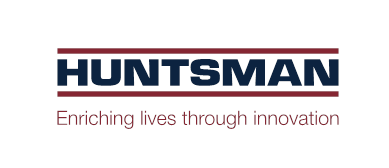
Full Recycling of Epoxy based Thermoset Composites
A full Composites-Recycling Technology is required to recover energy-efficiently not only the fibres, also valuable chemical ccomponents from the cured epoxy resin.
More stringent legislation, i.e. EU automotive directive requiring recycling quotas of 95% from the car, or the need for lowering CO2 footprints lead to the requirement of the recycling of the polymer, not only the fibres of the composite.
Lightweight composite solutions are therefore under very high risk to be produced in Europe. So, a significant part of our business is on risk – main portion of the resins going into composite applications are produced in our plant in Monthey, Switzerland.
Epoxy based composites are designed for longevity, exhibiting high thermal and chemical resistance (specifically the structural composite parts for airplanes such as wings, turbine blades, fuselage…) which are therefore difficult to recycle. No effective recycling solution is yet in place or proven to be commercially viable, which can be upscaled or industrialized.
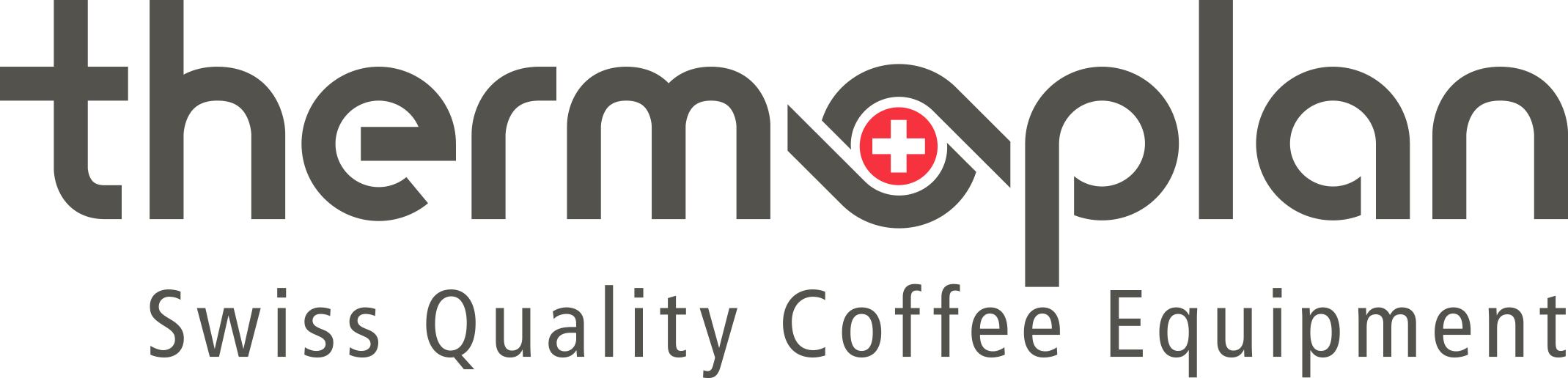
Next generation sustainable coffee vending machines
Thermoplan produces market-leading coffee vending machines for corporate clients. The enormous workload places high demands on the design, materialization and construction of the machines. The next generation should be more sustainable without having to compromise on use. To achieve this, completely new concepts must be developed for the use of materials, construction methods and assembly of the machines. The goal is to significantly improve the CO2 footprint. The start is to be made with a door that must consist mainly of recycled plastic, where completely new and disruptive concepts are sought, and a clear benefit in terms of environmental impact has to be proven.
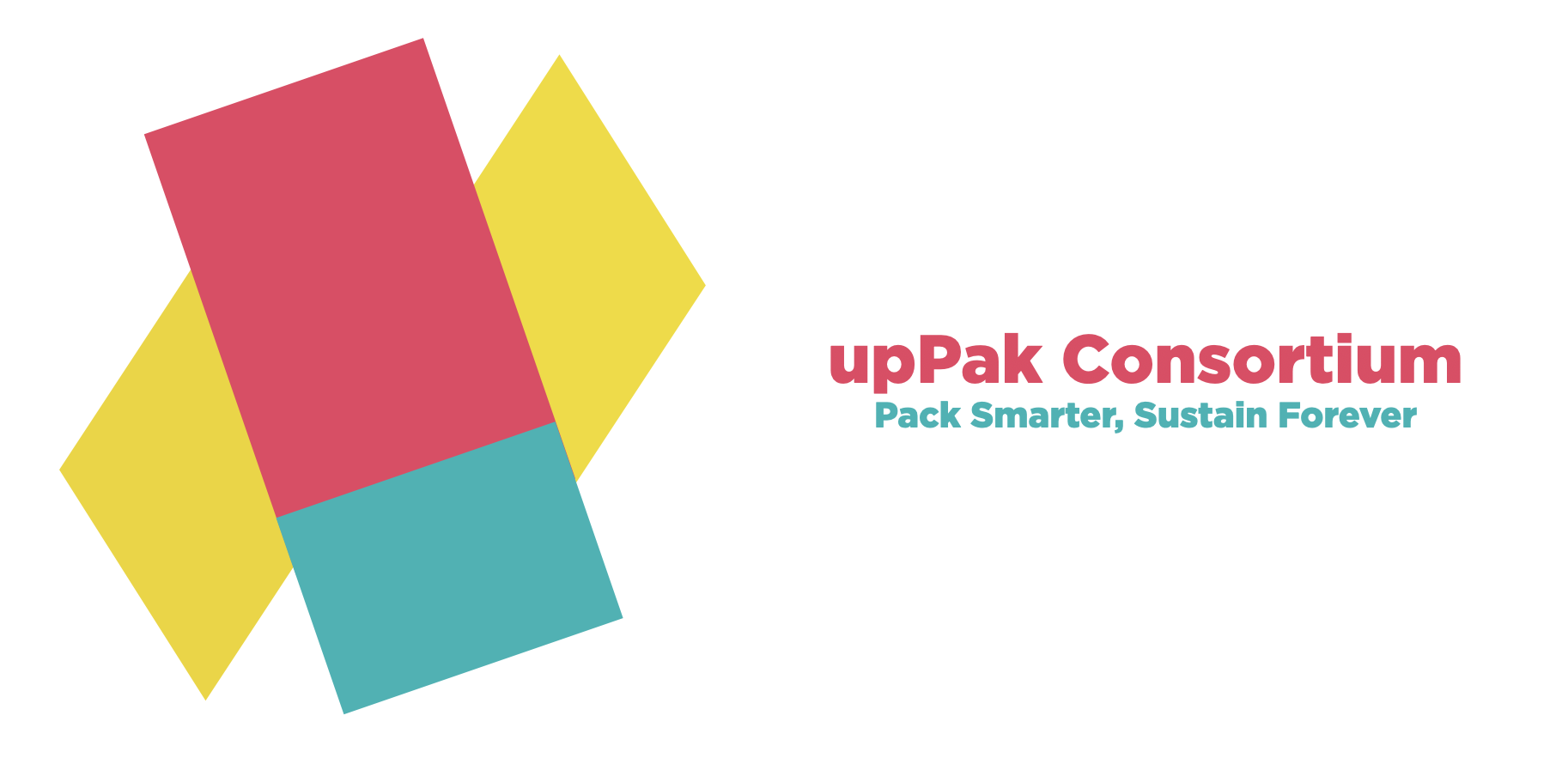
upPak Consortium
We are upPak. A Swiss based consortium committed to a common goal: to develop and implement chitosan based packaging solutions for food products.
By upcycling existing byproducts from the sea-food processing industry, we are able to divert precious raw materials from landfills and reintegrate them into the food system. Developing alternatives to PE coatings serves the environmental by reducing our dependancy on fossil fuels and phasing out micro-plastics from our supply chains.
As an abundant natural resource, second only to cellulose, chitosan bio-polymers are completely bio-degradable and can allow for seamless recycling of paper without the need for separating packaging from coating.
The core principle of our strategy is to rally critical partners along the value chain. By providing an aligned ecosystem that profits from shared-innovation and novel business opportunities, we look to achieve a truly inspiring product that will be available in market by 2026.
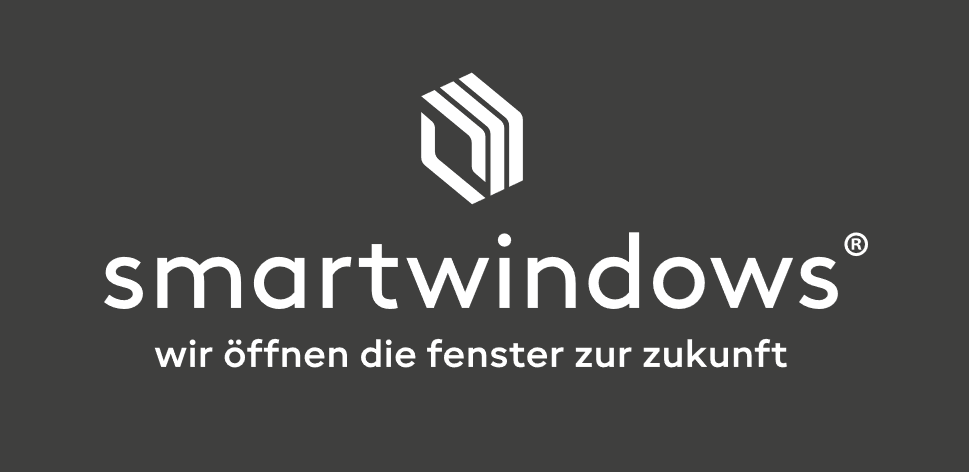
A Window to Zero Emission Society
Background
The reduction of energy losses in buildings are amongst the most important objectives for the transformation to a zero-emission society. The impact of plastic windows is significant, as they combine highest ecological ratings with shorter return on investment and low maintenance cost. The Swiss windows market is estimated to 1.5 Mrd CHF per year, with a growing share of 50% of plastics windows. The roof and the windows are the primary targets to reduce energy losses of buildings. In average the replacement of windows results in 25% reduction of CO2 emission. With the increasing importance of plastic windows, efficient circular solutions for window materials are becoming increasingly important.
Challenge and Innovation
Circular loops for a second life of the plastic-, metal-, and glass parts of the window need to be improved in terms of quality, yield, and efficiency. Radical innovations shall lead to such improvements:
- Business transformation: The new decommissioner (building company) becomes a supplier of secondary raw materials. How can digital technologies support this transformation and ensure the decommissioner and his employees meet the quality and traceability requirements.
- Technology innovation: Develop smart technologies for a decentralized separation into high quality plastic-, metal– and glass fractions for a direct, efficient, full truck load transportation to the recycling plants. This may include AI, visual recognition as well as smart mechanical solutions.
Call for research partners to join the challenge.
We are looking for research partners able to combine new technologies, such as digital technologies with the needs of secondary feedstock. They should have means to prove concepts and to demonstrate the feasibility of new technologies on the smallest industrial scale.
Testimonials and Success Stories
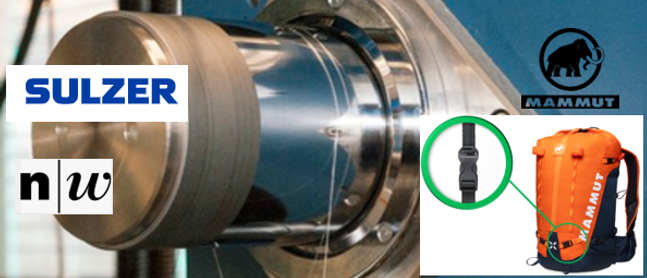
Sulzer / Mammut – Melt spinning of sustainable fibres for belts and straps in outdoor applications
Time to shine light on a milestone on our road to a more sustainable textile industry is being achieved through the collaboration of Sulzer, Mammut and FHNW. The project’s central focus is the development of more responsible solutions based on bio-based materials, addressing a critical issue – the prevalent use of petroleum-based materials that are neither environmentally friendly nor recyclable.
Sulzer, a provider of thermal separation and polymerization licenced technologies for bio-based polyesters such as polylactic acid (PLA), and Mammut, the Swiss outdoor brand as the end-user, have joined forces with FHNW to create a transformative solution. The project adopts a holistic approach, commencing with design thinking, considering end-user demands for more resourceful one-material solutions and moving backward to the spinning process and advanced polymer formulations.
Mammut’s commitment to the UN Fashion Industry Charter for Climate Action underscores the project’s climate-conscious foundation. They are determined to halve greenhouse gas emissions within the next decade and achieve net-zero emissions by 2050. The project aligns with Mammut’s endeavor to reduce carbon emissions across its value chain, promoting the transition to renewable energy sources.
The novelty of this project lies in its comprehensive approach, covering end-user requirements, processing, polymer formulation, and scaling. Initiated by Sulzer and FHNW, Mammut joined the team, enhancing the project’s strength and potential for success.
The project envisions substituting fossil-based polymers, currently consumed in Switzerland and the European Union, with bio-based materials. While the specific target market remains unspecified, the objective to reduce CO2 emissions and decrease fossil product use is clear.
This initiative brings promising benefits, aiming to reduce CO2 emissions, fossil waste, and the dependence on petroleum-based materials. It offers the potential to replace substantial volumes of petroleum-based textiles with more sustainable bio-based alternatives. The obstacles and risks include cost considerations, market acceptance, quality assurance, scaling production, and securing a reliable supply chain.
While the project’s details are clear, a comprehensive Life Cycle Assessment is needed to evaluate its full environmental impact, including raw material sourcing, production, usage, and waste treatment. The project paves the way for a more sustainable textile industry and aligns with the global shift towards more eco-conscious practices.
Sophie Renot, Mammut
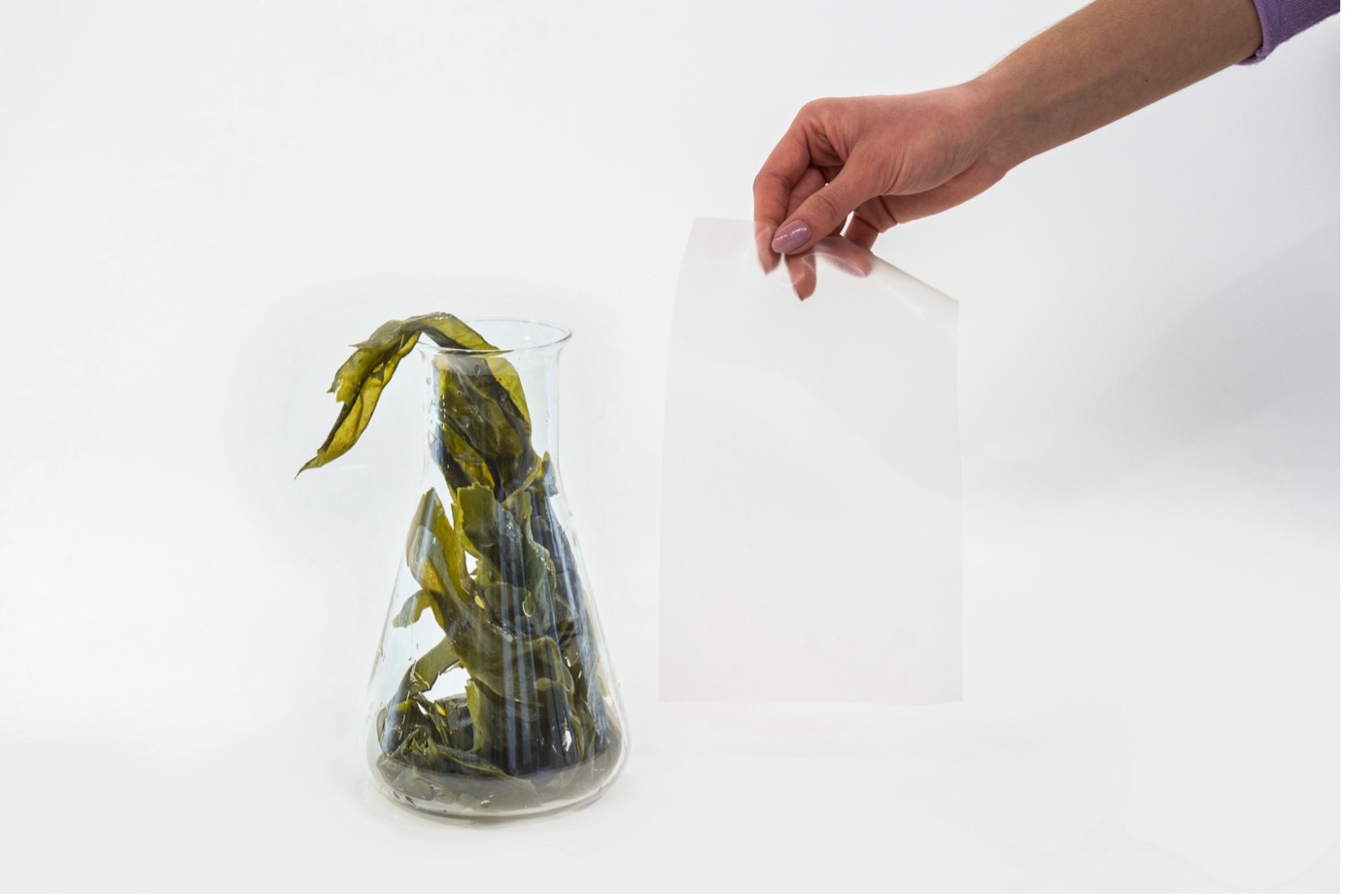
Noriware – Redefining sustainable packaging
Noriware, a Swiss start-up founded in 2022, has emerged as a beacon of hope in the fight against plastic pollution. Equipped with a ground-breaking technology developed in collaboration with ETH Zurich and FHNW, Noriware set out to revolutionise the packaging industry. Their goal? To find a long-term and sustainable solution to the global plastic problem. Their weapon of choice? Algae-based packaging materials that can be 100% composted at home, and in an unprecedented timeframe. Noriware’s journey began with a serendipitous encounter in Mexico, where HSG student Jessica Farda noticed an abundance of algae on the beach. This simple observation gave her an idea. Could algae be the answer to our plastic problem? Jessica returned to her studies and immersed herself in research on the potential of algae as a sustainable resource for bioplastics. In the humble surroundings of her kitchen, she conducted experiments that would lead to a potential breakthrough in the search for environmentally friendly packaging. In September 2021, she joined forces with the Department of Materials Science at ETH Zurich, providing important expertise in materials science. In May 2022, Jessica’s path took a decisive turn when she met her co-founder Stefan Grieder, resulting in a collaboration with the Institute of Plastics Technology and Engineering at the FHNW thanks to the Innovation Booster “Plastics for Zero Emissions” award, adding essential expertise in polymer chemistry and engineering. In September 2022, Noriware AG was officially founded in Aargau and, with the substantial support of the Aargau Research Fund, the cooperation with the University of Applied Sciences continued. In May 2023, the start-up founders succeeded in securing a pre-seed financing round of over 1 million Swiss francs, enabling them to expand their own laboratory infrastructure in Lupfig, Aargau, and launch larger pilot projects with industry partners. With the support of Professor Dr. Markus Grob and Prof. Dr. Christian Brauner, Noriware is well on its way to even greater success. Noriware will continue to expand its product portfolio and contribute to a sustainable future. The company is on its way to redefine the packaging industry and to stimulate a change in corporate thinking for the benefit of the environment, people and the economy.
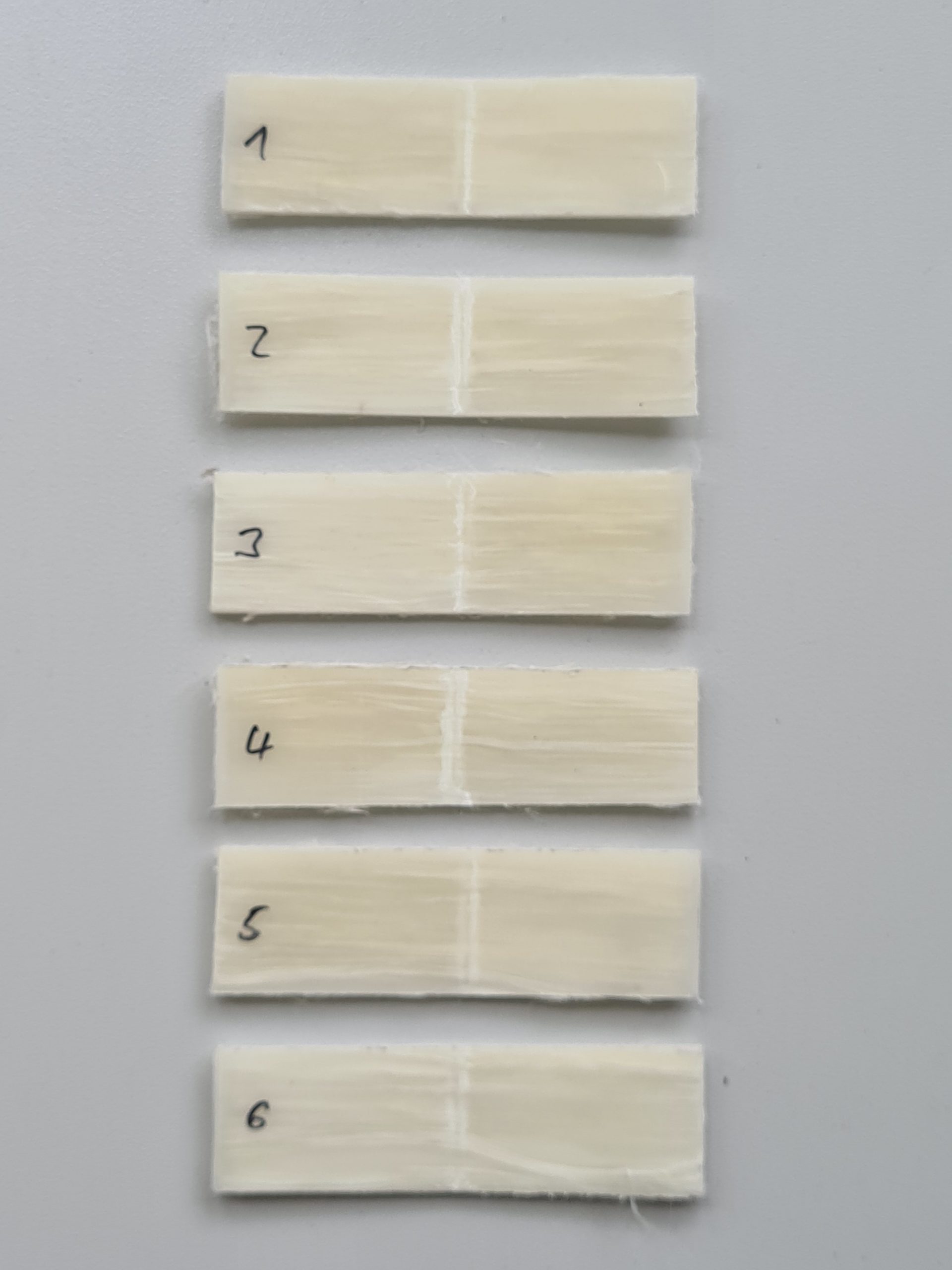
Ensinger Composites Schweiz GmbH – Self reinforced bio-based polymers
This forward-thinking project embarks on the mission to make composite materials more sustainable through the development of self-reinforced biobased polymers. The approach underpinning this endeavour is the concept of “self-reinforced polymer composites” (SRPCs) or “all-polymer” composites, where a polymer matrix is reinforced by means of fibres of the same polymer. The ingenious aspect of SRPCs is that they offer enhanced fiber-matrix interfacial adhesion and, more crucially, complete recyclability without the need for the arduous separation of fibre and matrix.
The project’s thematic focus revolves around creating biobased SRPCs, introducing a novel dimension to sustainable composite recycling. The capacity to use entirely biodegradable bio-sourced composite materials promises to optimise waste disposal, offering a recycling solution where none existed before. The degree of innovation here is exceptionally high.
The impact of this initiative extends to the heart of the composite industry. As the demand for lightweight design surges, the use of traditional composites like glass and carbon fibers with thermoset matrices presents significant recycling challenges. The project’s approach opens the door to the development of 100% recyclable materials.
Moreover, the secondary objective of developing not just bio-sourced but also bio-degradable materials shifts the need for recycling to composting, particularly vital for components where traditional recycling is impractical or uneconomical.
The funds allocated to this project will facilitate the melt spinning of selected polymers, paving the way for critical spinning trials, fibre processing, characterization, and comparison to the requirements set by Ensinger, the project partner. This collaborative process will enable further refinements in polymer selection and process parameters, ultimately leading to the production of fibres suitable for the composite industry.
The project is structured into work packages that include polymer selection and characterization, melt spinning of fibres, feasibility testing for self-reinforced polymer plates, and the development of process routes for textile production. Completion of WP2 and WP3 is vital in demonstrating the potential of self-reinforced polymers for composite materials.
In sum, this project is a pioneering step towards the future of sustainable, recyclable composite materials, bringing innovative solutions to the core of the composite industry.
Niccolo Pini, Ensinger Composites Schweiz GmbH
![1688970335674[97]](https://plastics4zeroemission.ch/wp-content/uploads/2023/10/168897033567497.jpg)
V Carbon – Recycled carbon fibres for Sports Industry
In the pursuit of innovation, V Carbon GmbH stands as a pioneering force in the realm of recycled carbon fibre (rCF) intermediates. Their latest venture focuses on establishing a market for rCF yarn-based products, known for their cost-effectiveness and remarkable mechanical performance, making them ideal candidates for application in load-bearing structures.
At the heart of this endeavour lies the objective of winding tubular structures with yarn and a thermoset matrix to demonstrate their suitability for load-bearing applications. The technical innovation crucial to this project is the development of a suitable impregnation and winding method for recycled yarn, a task of immense significance in the world of sustainable composites.
The project’s objectives encompass demonstrating the feasibility of rCF yarn winding with thermoset matrix systems. This involves defining optimal processing parameters for winding and yarn impregnation, assessing the mechanical properties of tubular wound structures, and creating a benchmark application.
The benchmark application, a high-performance racing bicycle frame, will serve as a testimonial to the project’s capabilities and achievements. Collaborating with esteemed German companies, SPIN Siebert & Schörner GbR and CG TEC Carbon und Glasfasertechnik GmbH, further underscores the commitment to excellence and practicality by design thinking methods.
V Carbon GmbH’s project not only promises a groundbreaking development in the realm of rCF but also emphasizes the importance of sustainable innovation and its impact on load-bearing structures. This initiative sets the stage for advancements that have the potential to revolutionize the composite industry by paving the way for cost-effective, mechanically robust rCF yarn-based products.
Leo Walker, V Carbon
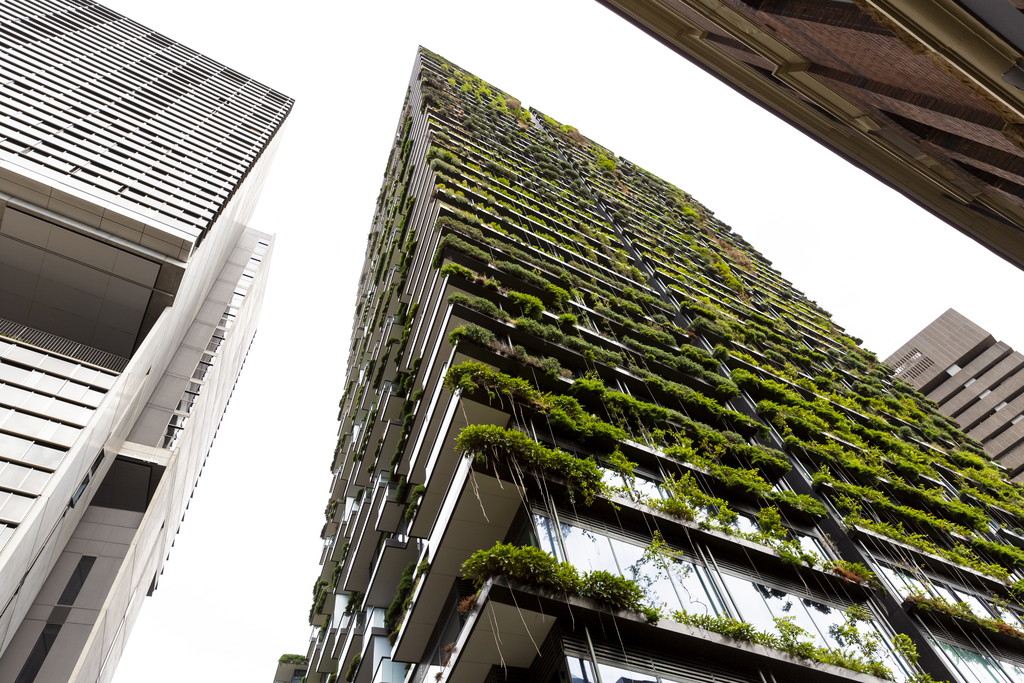
Sika Technology AG – Carbon Green
In the ever-evolving landscape of sustainable materials, SIKA and the Institutes of Biomass and Polymer Engineering at FHNW have embarked on a groundbreaking collaboration. Their mission: to usher in an innovative solution by replacing carbon black with biochar in various bonding solutions of SIKA.
The project’s foundation lies in a critical evaluation of current sealants formulated with recycled carbon black, which have fallen short of desired standards. Encouragingly, raw biochar grades have emerged as promising alternatives from both pigmentation and reinforcement perspectives.
The innovation at hand is two-fold. Firstly, it involves the introduction of biochar, a negative emission material originating from waste biomass streams. This not only promotes sustainability but also establishes a carbon-creditable business model, aligning with SIKA’s goal of environmental responsibility. Secondly, the collaboration between SIKA and the Institutes of Biomass and Polymer Engineering offers a holistic approach to efficiently address the entire process, from biochar production to the final product, facilitating swift prototyping.
The potential impact of this initiative is immense. By replacing carbon black with biochar, SIKA has the potential to save a remarkable 37.4 million tons of CO2 equivalent emissions over the next years. Such a solution is unprecedented in the market, and its positive ripple effects can extend beyond bonding solutions to other sectors, including automotive and wind turbines.
Methodologically, this collaboration leverages the expertise and equipment of FHNW in biochar production and polymer engineering, offering a unique advantage for SIKA. The project’s structure, from screening different biochar materials to in-house biochar production and evaluation, ensures a comprehensive approach.
Moreover, this project promotes gender and diversity inclusion, further enhancing its value and potential for success. Together, SIKA and the Institutes of Biomass and Polymer Engineering are paving the way for a more sustainable and environmentally responsible future.
The Carbon Green team, Sika Technology AG
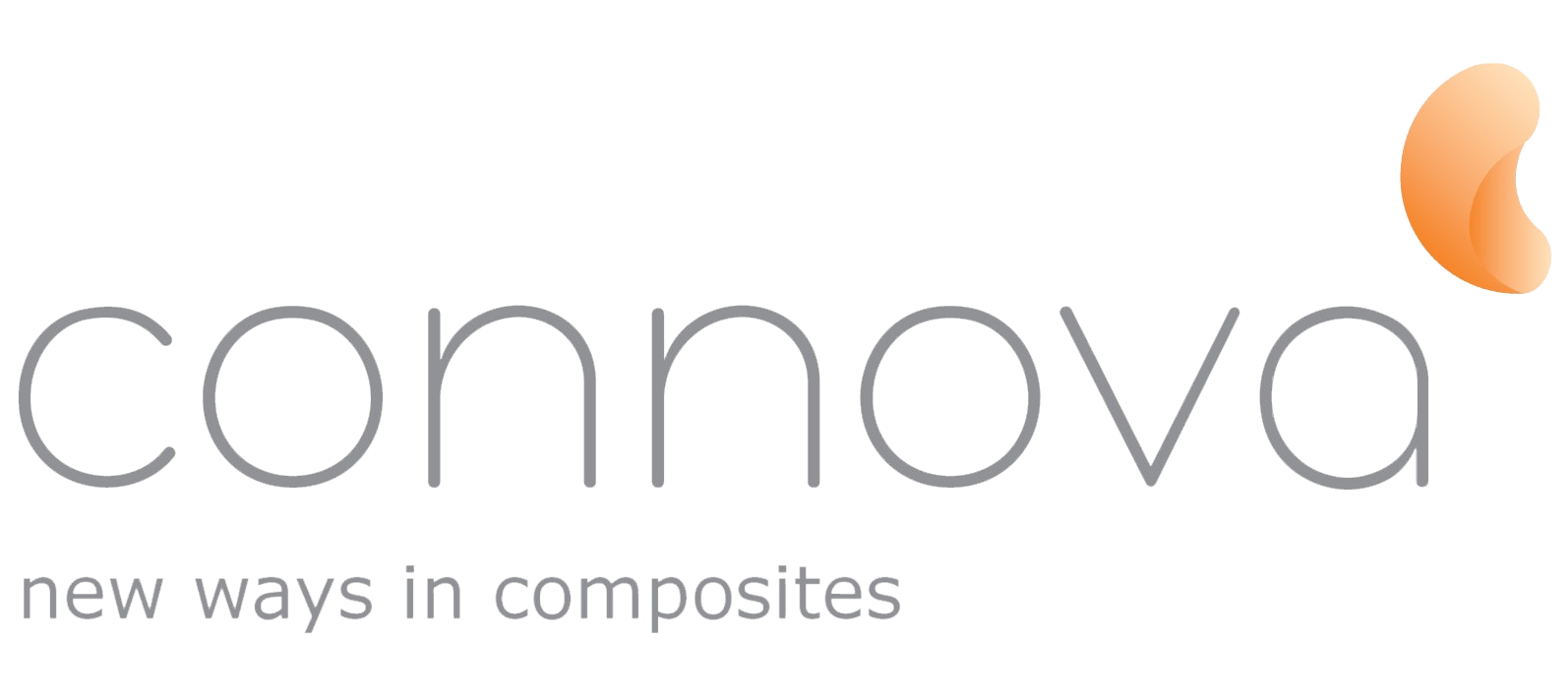
Connova – Reversible hybrid metal-composite connections for sustainable assemblies
A groundbreaking project, driven by Connova, OST, and FHNW, is poised to transform the realm of composite materials. Focused on reversible techniques for joining and later recycling thermoset composites, it champions innovation and circularity. This initiative not only aims to cut weight and fuel consumption but, more importantly, to slash CO2 emissions by finding reliable, cost-effective methods for joining fiber-reinforced composites. These techniques facilitate repair, reuse, re-design, and recycling, substantially reducing the CO2 footprint of these energy-intensive components.
The project embarks on a pioneering journey to explore structural joining techniques for thermoset composites, designed for easy detachment at the end of their lifespan. Novel methods include debonding epoxy adhesives with embedded iron particles, a potentially groundbreaking solution, and the innovative use of thermoplastic joining for thermosets.
Collaboration between Connova, OST, and FHNW emerged in response to Connova’s challenge, demonstrating the power of the Innovation Booster platform to bring diverse expertise together. Connova, as an implementation partner, stands to gain invaluable knowledge and tools to offer customers highly efficient, recyclable thermoset composite solutions, creating a competitive edge and opening new avenues for sales.
The project also aligns with Connova’s sustainability goals, promoting the extended lifespan, repair, and reuse of components, as well as efficient recycling, ultimately reducing the demand for petrochemical resources and lowering CO2 emissions.
With FHNW and OST contributing their expertise and laboratory facilities, the project ensures a robust methodological approach to address the industry’s needs.
The project’s scope includes evaluating various joining technologies for reversible composite-composite or composite-metal connections, with work packages structured to achieve these goals. Successful completion of WP1 and WP2 is pivotal in demonstrating the potential of the proposed joining and disassembly concepts.
The project signifies a remarkable stride towards achieving sustainability and circularity in the composite materials domain, bringing innovative, environmentally conscious solutions to the forefront.
Sebastian Preiss, Connova